Что такое 5S? Система 5S. Система 5с
14 Октябрь 2011 Евгений Неделин Просмотров:Что такое система 5S
Система 5S – это система организации рабочего места, которая позволяет значительно повысить эффективность и управляемость операционной зоны, улучшить корпоративную культуру, повысить производительность труда и сохранить время. Это первый шаг на пути к созданию бережливого предприятия и применению других инструментов системы менеджмента компании Toyota.
Краткая история системы 5S
В Японии системный подход к организации, наведению порядка и уборке рабочего места возник в послевоенный период, точнее, к середине 50-х годов ХХ века. В то время японские предприятия были вынуждены работать в условиях дефицита ресурсов. Поэтому они разработали для своего производства метод, при котором учитывалось все и не было места никаким потерям.
Первоначально в японской системе было только 4 действия. Слова, обозначающие эти действия, в японском языке начинаются с буквы
- Seiri (整理)– Sorting – сортировка.
- Seiton (整頓) – Straighten or Set in Order –рациональноерасположение.
- Seiso (清掃) – Sweeping – уборка.
- Seiketsu (清潔) – Standardizing – стандартизация работ.
Позже добавилось пятое действие, его назвали Shitsuke (躾) – Sustaining – поддержание достигнутого и совершенствование, и оно завершило цепочку элементов, которые теперь известны как 5S.
Сейчас система 5S обладает фундаментальной мощью для того, чтобы изменять рабочие места и вовлекать в процесс улучшений всех работников.
В систему 5s входят пять действий:
1) Сортировка – означает, что вы высвобождаете рабочее место от всего, что не понадобиться при выполнении текущих производственных операций.
Рабочие и руководители часто не имеют привычки избавляться от предметов, которые больше не нужны для работы, сохраняя их поблизости «на всякий пожарный случай». Обычно это приводит к недопустимому беспорядку или к созданию препятствий для перемещения в рабочей зоне. Удаление ненужных предметов и наведение порядка на рабочем месте улучшает культуру и безопасность труда. Чтобы более наглядно продемонстрировать, сколько лишнего скопилось на рабочем месте, можно на каждый предмет-кандидат на удаление из рабочей зоны повесить красный ярлык (флажок).
Все сотрудники вовлекаются в сортировку и выявление предметов, которые:
- должны быть немедленно вынесены, выброшены, утилизированы;
- должны быть перемещены в более подходящее место для хранения;
- должны быть оставлены и для них должны быть созданы и обозначены свои места.
Необходимо чётко обозначить «зону красных ярлыков» предметов с красными флажками и тщательно её контролировать. Предметы, остающиеся нетронутыми свыше 30 дней, подлежат переработке, продаже или удалению.
2) Рациональное расположение – означает определить и обозначить «дом» для каждого предмета, необходимого в рабочей зоне. Иначе, если, например, производство организовано по сменам, рабочие разных смен будут класть инструменты, документацию и комплектующие в разные места. В целях рационализации процессов и сокращения производственного цикла крайне важно всегда оставлять нужные предметы в одних и тех же отведённых для них местах. Это ключевое условие минимизации затрат времени на непродуктивные поиски.
3) Уборка (содержание в чистоте) – значит обеспечить оборудованию и рабочему месту опрятность, достаточную для проведения контроля, и постоянно поддерживать её.
Уборка в начале и/или в конце каждой смены обеспечивает немедленное определение потенциальных проблем, которые могут приостановить работу или даже привести к остановке всего участка, цеха или завода.
4) Стандартизация
– это метод, при помощи которого можно добиться стабильности при выполнении процедур первых трех этапов 5S – значит разработать такой контрольный лист, который всем понятен и прост в использовании. Продумать необходимые стандарты чистоты оборудования и рабочих мест, и каждый в организации должен знать, как это важно для общего успеха.5) Совершенствование – означает то, чтобы выполнение установленных процедур превратилось в привычку
Мероприятия, лежащие в основе 5S (сортировка, рациональное расположение, уборка, стандартизация и совершенствование), абсолютно логичны. Они представляют собой базовые правила управления любым продуктивно работающим отделом. Однако именно системный подход, который система 5S применяет к этим мероприятиям, и делает ее уникальной.
Обратите внимание на программу тренингаописание, особенности, принципы и отзывы
Руководитель любого предприятия, независимо от сферы деятельности, мечтает, чтобы прибыль росла, а производственные затраты оставались неизменными. Добиться такого результата помогает система «5С» на производстве (в английском варианте 5S), основывающаяся только на рациональном использовании внутренних резервов.
Создавалась эта система не с чистого листа. Нечто подобное еще в конце XIX века предлагал американец Фредерик Тейлор. У нас в России этим занимался ученый, революционер, философ и идеолог А.А. Богданов, издавший в 1911 году книгу о принципах научного менеджмента. На основе изложенных в ней положений в СССР внедряли НОТ, то есть научную организацию труда. Но наиболее совершенной стала предложенная японским инженером Тайити Оно и внедренная им на заводе Toyota Motor система «5С» на производстве. Что это такое, и почему японская система стала такой популярной?
Дело в том, что в ее основе лежит простой принцип, не требующий затрат. Он заключается в следующем — каждый работник, от уборщицы до директора, должен максимально оптимизировать свою часть в общем рабочем процессе. Это приводит к увеличению прибыли производства в целом и к росту доходов всех его сотрудников. Сейчас эстафету внедрения системы «5С» подхватили предприятия во всем мире, включая Россию. В этой статье мы попытаемся убедить скептиков в том, что японское ноу-хау действительно работает, причем абсолютно в любой сфере деятельности.
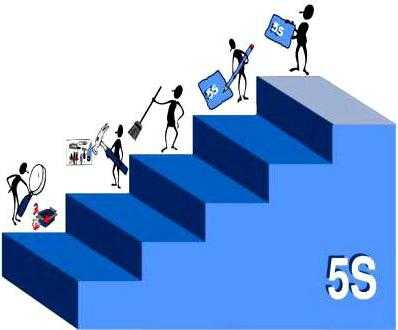
Система «5С» на производстве, что это такое
Международное 5S расшифровывается, как пять шагов («шаг» по-английски step). Некоторые экономисты и пропагандисты нового отношения к труду объясняют название пятью японскими постулатами, последовательно внедряемыми в системе 5S: сэири, сэитон, сэисо, сэикэцу и сицукэ. Для нас ближе и понятнее наши родные «5С» — пять последовательных шагов, которые нужно выполнить, чтобы добиться процветания своего производства. Это:
1. Сортировка.
2. Соблюдение порядка.
3. Содержание в чистоте.
4. Стандартизация.
5. Совершенствование.
Как видим, ничего сверхъестественного система «5С» на производстве не требует. Возможно, именно поэтому к ней пока можно встретить недоверие и несерьезное отношение.
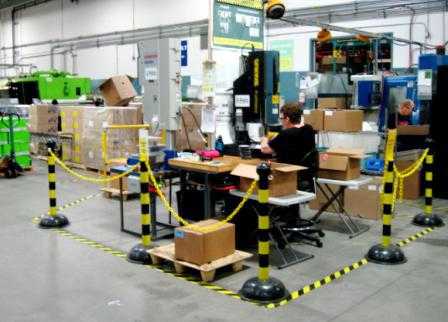
Этапы создания системы
Мудрый японец Тайити Оно, который, благодаря внедрению на заводе по производству «Тойот» своих методик, сумел дослужиться от инженера до генерального директора, обратил внимание, как много потерь происходит из-за различных неувязок и накладок. Например, на конвейер не поставили вовремя какие-нибудь мелкие винтики, и в результате встало все производство. Или наоборот, деталей подали с запасом, они оказались лишними, и в результате кому-то из сотрудников пришлось везти их обратно на склад, а значит, тратить на пустую работу свое время. Тайити Оно разработал концепцию, которую назвал «точно в срок». То есть на конвейер теперь поставлялось ровно столько деталей, сколько нужно.
Можно привести и другие примеры. Система «5С» на производстве также включала в себя концепцию «канбан», что по-японски значит «рекламная вывеска». Тайити Оно предложил на каждую деталь или каждый инструмент цеплять так называемую бирку «канбан», в которой давалась вся необходимая информация по детали или инструменту. В принципе, она применима к чему угодно. Например, к товарам, медикаментам, папкам в офисе. Третьей концепцией, на которой основывается система «5С» на производстве, стало понятие «кайдзен», означающее непрерывное совершенствование. Придумывались и другие концепции, которые подошли лишь для узкоспециализированных производственных процессов. В этой статье мы их рассматривать не будем. В итоге всех опробованных на практике нововведений и сформировалось 5 шагов, применимых к любому производству. Разберем их подробно.
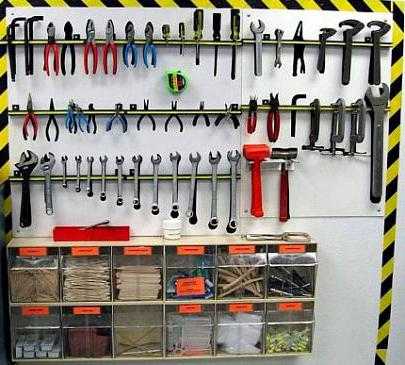
Сортировка
У многих из нас на рабочих столах скапливаются предметы, которые, в принципе, не нужны. Например, старые формуляры, не используемые файлы, черновики расчетов, салфетка, на которой стояла чашка кофе. А среди этого хаоса могут находиться нужные файлы или документы. Основные принципы системы «5С» подразумевают оптимизировать свой рабочий процесс, то есть сделать так, чтобы не тратилось время на поиск нужных вещей среди завалов ненужного. Это и есть сортировка. То есть на рабочем месте (возле станка, на столе, в мастерской – где угодно) все предметы раскладываются на две стопки – нужное и ненужное, от которого необходимо избавиться. Далее все нужное раскладывается на следующие стопки: «используется часто и постоянно», «используется редко», «почти не используется». На этом сортировка закончена.
Соблюдение порядка
Если просто разобрать предметы, толку не будет. Нужно эти предметы (инструменты, документы) разложить в таком порядке, чтобы используемое постоянно и часто очутилось на виду или так, чтобы его можно было быстро взять и легко положить назад. То, что используется редко, можно отправить куда-нибудь в ящик, но к нему нужно прикрепить бирку «канбан», с тем, чтобы через время можно было легко и безошибочно его найти. Как видим, система «5С» на рабочем месте начинается с самых простых шагов, но на деле она оказывается очень эффективной. А кроме того, она повышает настроение и желание трудиться.
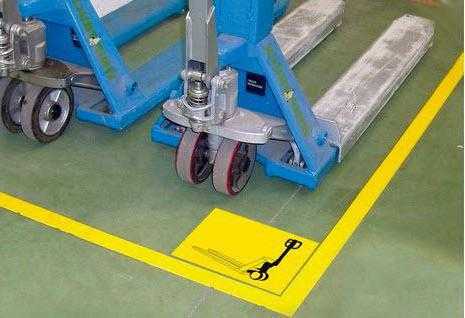
Содержание в чистоте
Этот третий шаг является для многих самым логичным. Соблюдать чистоту нас учат с детства. На производстве она тоже необходима, причем, чистыми должны быть не только столы офисных работников или шкафы в учреждениях общепита, но и станки, подсобные помещения уборщиц. В Японии сотрудники бережно относятся к своим рабочим местам, трижды в день их убирают – с утра перед работой, в обеденный перерыв и вечером, по окончании трудового дня. Кроме того, у них на предприятиях введена специальная маркировка участков, позволяющих соблюдать на производстве порядок, то есть разными цветами отмечены участки готовой продукции, складирования определенных деталей и так далее.
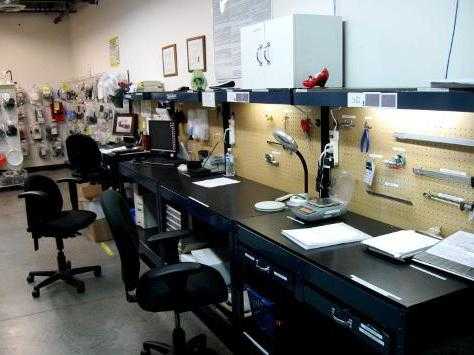
Стандартизация
Принципы стандартизации придумал еще Тайити Оно. Широко использует их и современная система 5S. Управление производством, благодаря стандартизации, получает замечательный инструмент контроля за всеми процессами. В результате быстро устраняются причины отставания от графика и исправляются ошибки, приводящие к выпуску некачественной продукции. На заводе Toyota Motor стандартизация выглядела так: мастера составляли ежедневные планы работ, на рабочих местах вывешивались точные инструкции, в конце трудового будня специальные работники проверяли, какие за день произошли отступления от плана и почему. Это и есть основное правило стандартизации, то есть точные инструкции, планы работ и контроль за их выполнением. Сейчас на многих предприятиях, например, на заводах ENSTO в Эстонии, вводится премиальная система работников, четко выполняющих положения системы «5С» и на основе этого повышающих свою производительность, что является отличным стимулом принять эту систему, как образ жизни.
Совершенствование
Пятый шаг, на котором завершается система «5С» на производстве, основан на концепции кайдзен. Она означает, что все работники, независимо от занимаемой должности, должны стремиться усовершенствовать процесс работы на вверенном им участке. Философская суть кайдзен заключается в том, что вся наша жизнь каждый день становится лучше, а коль работа – это часть жизни, она тоже не должна оставаться в стороне от улучшений.
Поле деятельности тут широкое, ведь пределов у совершенства не существует. Согласно понятиям японцев, работники сами должны хотеть улучшить свой производственный процесс, без указаний и принуждений. Сейчас во многих организациях создаются команды рабочих, следящих за качеством продукции, обучающих своему положительному опыту других, помогающих добиваться совершенства.
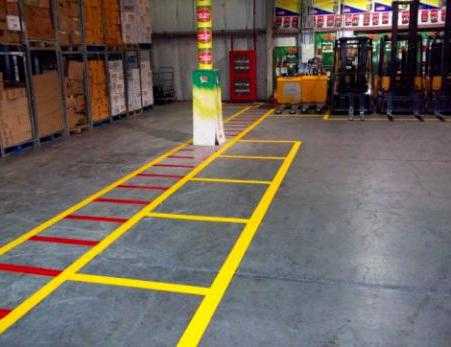
Основные ошибки
Чтобы система «5С» начала работать, мало ее организовать или взять на работу сотрудников, которые будут заставлять своих коллег ее внедрять. Тут важно, чтобы люди осознали полезность этого новшества и приняли его как стиль жизни. Внедрение системы «5С» в России на производстве сталкивается с трудностями именно по причине того, что наш русский менталитет отличается от японского. Для многих наших производств характерно следующее:
1. Работники, особенно если для них нет поощрительных стимулов, не стремятся увеличить прибыль предприятия. Они спрашивают, зачем стараться сделать начальника еще богаче, если у него и так все есть.
2. Сами руководители не заинтересованы во внедрении системы «5С», потому что не видят в ней целесообразности.
3. Многие директивы, «спускаемые сверху», привыкли выполнять только для «галочки». В Японии наблюдается совсем другое отношение к своему труду. Например, тот же Тайити Оно, внедряя систему «5С», думал не о личной выгоде, а о выгоде компании, в которой он был всего лишь инженером.
4. На многих предприятиях внедряется насильно система «5С». Бережливое производство, подразумевающее устранение потерь всех видов (рабочего времени, сырья, хороших работников, мотивации и прочих показателей) при этом не получается, так как работники начинают на подсознательном уровне противиться нововведениям, что в итоге сводит все старания к нулю.
5. Руководители, внедряющие систему, не полностью понимают ее суть, из-за чего возникают сбои в налаженных процессах производства.
6. Стандартизация часто перерастает в бюрократию, хорошее дело обрастает указаниями и директивами, которые только мешают работе.
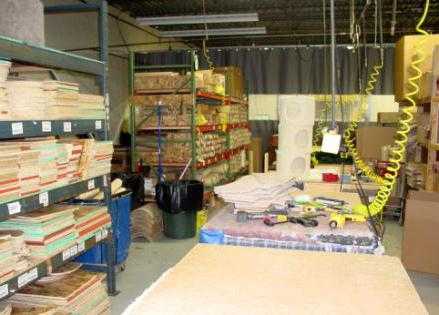
Отзывы
Россияне, у кого введена система «5С» на производстве, отзывы об этом новшестве оставляют весьма неоднозначные. Отмечаемые плюсы:
- приятнее находиться на рабочем месте;
- не отвлекают от работы ненужные мелочи;
- более четко идет рабочий процесс;
- снизилась усталость в конце смены;
- немного возросла зарплата за счет увеличения производительности труда;
- снизился производственный травматизм.
Отмечаемые минусы:
- проводя сортировку, заставляют выбрасывать все подряд;
- стандартизация привела к увеличению бюрократии;
- введение системы «5С» не на всех участках предприятия усугубило проблемы;
- постановка на первое место системы «5С» отодвинула на второй план такие важные вопросы, как нехватка запчастей.
fb.ru
Система 5С – Основа повышения производительности
О предназначении системы 5С, ее основных принципах, методологии и первых удачных результатах внедрения расскажет IamBuilding в серии статей посвященной данной тематике. Все статьи будут касаться проектов проведения 5С на складе, 5С в офисе и 5С на транспорте.
Данная статья является вводной частью в данную систему и позволит в целом ответить на наиболее часто задаваемые вопросы.
Постоянное совершенствование процессов (любых процессов) позволяет компаниям использующим бережливые технологии оставаться лидерами рынка и легче преодолевать различные экономические ситуации которые происходят в стране. Знание и умение применять принципы и подходы бережливых технологий позволяют более гибко перестраиваться под воздействием внешних факторов, таких как требования Клиентов или изменение требований ранка в целом.
Что такое система 5С?
Существует очень разное понимание системы 5С. Некоторые компании понимают 5С как простое наведение порядка: подмести рабочее место, разложить бумаги по папкам, сделать полки, организовать хранение на этих полках, сделать разметку на полу и так далее. Конечно, в 5С это все присутствует. Но это лишь то, что видно со стороны.
Эти видимые изменения очень хорошо воспринимаются, но к настоящему повышению производительности и достижению цели это обычно не имеет отношения.
Необходимо помнить! 5С организовывается для достижения конкретных целей:
· стабилизации процесса;
· организация эффективного рабочего места;
· устранение действий, не добавляющих ценности и мешающих выполнять работу.
Система 5С также позволяет последовательно выявлять и решать проблемы с качеством и производительностью, она получила название от первых букв пяти русских слов:
· Сортировка;
· Свои места для всего;
· Содержание в чистоте;
· Стандартизация;
· Самодисциплина/совершенствование.
Таким образом, система 5С – один из инструментов базовой стабилизации и направлена она на реализацию принципа «точно вовремя».
— Какие возможности открывает система 5С?
Здесь есть две основные выгоды.
Одна из них – выгода для Компании. Применение принципов 5С на постоянной основе позволяет снизить все имеющиеся издержки и потери при выполнении операций, что в свою очередь увеличивает производительность процесса, снижает количество ошибок которые могут возникать в процессе.
Другая выгода – выгода для сотрудников. Процесс совершенствования по системе 5С позволяет вовлечь сотрудников и привить им культуру труда и бережливого подхода к рабочим процессам, в результате которого сотрудники приобретают новые навыки, знания и опыт эффективного применения 5С. Сотрудники, знающие и умеющие применять принципы и подходы бережливых технологий, способны более гибко перестраиваться под воздействием новых требований рынка и клиентов.
Кроме того, повышение качества и скорости обслуживания должно сказываться на благосостоянии сотрудников в этих процессах.
— Где можно использовать принципы 5С?
Система 5С одинаково эффективна и в офисе, и на складе, и производственном цеху и на транспорте. Все зависит от специфики деятельности организации и приоритетности решаемых задач. В разделе «Бережливые технологии» мы разберем подход к реализации 5С в различных сферах деятельности, но начнем с 5С реализации принципов системы 5С на складе.
Офисные, производственные и транспортные операции конечно, тоже влияют на качество, производительность и, соответственно, на конечную цель которую компании ставят перед собой. Но к офисным процессам мы приступим в следующих статьях.
Примеры потерь в офисе и на складе
N |
Виды потерь |
Склад |
Офис |
1 |
Перепроизводство |
Скомплектованные заказы не уезжают на доставку из-за малой суммы заказа |
Составление ненужных отчетов |
Скомплектованные заказы на самовывоз не забираются своевременно Клиентом |
Большое количество документов на отгрузку |
||
Ожидание готовых заказов на складе, до момента доставки |
Предоставление информации в большем количестве, чем требует Клиент |
||
2 |
Транспортировка |
Допоставка рекламационного товара |
Поездка к Клиенту для переподписания документов |
Вытеснение и комиссионирование товаров для проведения комплектации |
Доставка товара Клиентам выездными менеджерами |
||
Возврат рекламационного товара |
Переоформление рекламационного товара |
||
3 |
Ожидание |
Ожидание поступления заказов на комплектацию |
Ожидание оплаты заказов Клиентами |
Ожидание определенного времени для доставки товара Клиентам |
Длительное изменение в процессах на системном уровне |
||
Ожидание прохождения всех заказов для формирования реестра доставки |
Ожидание ответов от поставщиков по поставкам и подтверждению брака. |
||
4 |
Излишние запасы |
Большое количество упаковочной тары |
Большие товарные запасы |
Много места занимает бракованный товар |
Ошибки в прогнозировании |
||
Хранение товара, на который отсутствует спрос (балласт) |
Излишние запасы канцтоваров |
||
5 |
Дефекты, переделки |
Замена рекламационного товара |
Перепечатка неправильно оформленных документов |
Несвоевременное размещение товара на адрес хранения (перепланировка) |
Корректировка прогнозов |
||
Ошибки при приеме и размещении товара |
Ошибки при выписке товара |
||
6 |
Излишняя обработка |
Дополнительный контроль при комплектации |
Создание дополнительных счетов по дефицитному товару |
Переработка бракованного товара |
Формирование актов отбраковки |
||
Упаковка товара |
Деление заявки на несколько счетов. |
||
7 |
Перемещения |
Отбор одного артикула с нескольких мест хранения (перемещения комплектовщика) |
Большой объем входящих сообщений и уведомлений на электронную почту |
Нерациональное размещение артикулов на места хранения (перемещение комплектовщика) |
Поиск и сверка данных в различных системах учета |
||
Дополнительные перемещения водителя штабелера при перемещении паллет с товаром после его приема |
Поиск товара при его отсутствии |
||
8 |
Не востребованный потенциал сотрудника |
Невостребованный потенциал сотрудников |
|
Слабое поступление предложений от сотрудников по улучшению своей работы и работы Компании |
|||
Отсутствие системы внутреннего обучения и развития сотрудников |
— Как и кем должно контролироваться соблюдение принципов 5С?
Любое начинание должно организовываться и поддерживаться руководством, которое однозначно должно быть вовлечено в процесс, давать импульс к достижению обозначенных целей.
Внедрение системы оценивается по Контрольным листам по каждому этапу 5С. Контрольный лист является документом как для самостоятельного контроля сотрудника, так и для контроля со стороны вышестоящих руководителей.
Если у Вас несколько складов или производственных участков и запуск 5С планируется производить параллельно на всех участках, то обязательно необходимо на высшем уровне сформировать координационную группу по реализации проекта 5С в Компании. У координационной группы должен быть распланирован график аудита каждого из участка, а в случаях если участки на которых производится запуск находится в разных географических частях света, то необходимо организовать возможность видеоконференций. Целью этих совещаний является выявление основных проблем и препятствий в реализации проекта 5С, а также внесение корректирующих мероприятий для более успешного и эффективного внедрения.
! обязательно учтите, что координационная группа должна именно видеть достигнутые результаты, а не просто о них слышать от докладчика. Поэтому в случаях аудита по средствам видеоконференции, необходима возможность трансляции различного материала, фотографии, презентации и т.д.
Мало просто достичь какого-то хорошего уровня 5С. Важно потом поддерживать систему в актуальном состоянии. И конечно, сразу возникает вопрос контроля и аудитов, а также вопрос реагирования на проблемы, которые позволяет выявлять система 5С. В этом смысле система 5С ничем не отличается от других методов управления. Здесь есть несколько важных моментов:
1. Обучение. Сотрудник должен понимать, что он делает и зачем это нужно. Для этого в компании должна быть разработаны методические рекомендации по каждому шагу 5С, в которых описаны принципы, применяемые на каждом из этих этапов, и отдельные ключевые организационные моменты. Дополнительно, рекомендуется использование различной литературы по тематике бережливых технологий.
2. Организация периодического контроля разных уровней. Работник (например, комплектовщик) должен контролировать сам себя, свои процессы, свое поведение. Непосредственный руководитель (например, начальник участка), контролирующий выполнение стандартизированной работы, должен проверить, насколько работник правильно понимает систему 5С и ее методы. При возникновении ситуаций, когда сотрудник не может выполнить стандарт или объективно оценить процесс и выявить проблему, руководитель должен прийти на участок, провести аудит и направить сотрудника на верный путь решения проблемы. Руководитель более высокого уровня (например, заведующий складом или директор) проверяет уже в свою очередь первого руководителя и так далее.
3. Дисциплина. Очевидно, что работники и руководители должны выполнять те обязательства по поддержанию системы, которые они на себя принимают. Воспитывать такую привычку в себе и коллегах следует целенаправленно.
— С какими проблемами наверное придется столкнуться?
В первую очередь следует сказать об организационных проблемах, так как не сразу удастся договориться, кто за что отвечает, и кто курирует проект на том или ином участке или в компании в целом.
В случаях если у Вас большая региональная сеть и запуск производится централизованно и одновременно, то столкнетесь с отсутствием поддержки рабочих групп на складах со стороны руководителей некоторых филиалов.
Так же одна из самых больших ошибок, это когда на каком либо производстве или складе руководитель (Который как мы говорили ранее должен быть основным идеологом системы на его филиале) делегирует ведение проекта по внедрению 5С подчиненным, а ведь это является принципиальной ошибкой в подходе по внедрению системы 5С и не только.
Придется менять стереотипы и видение сотрудников, так как довольно сложно будет объяснить на первом этапе, что является нужными предметами, а что нет. При попытке объяснить, что сортировка касается только конкретной зоны склада, в которой производится работа, сотрудники начинают думать, что если в целом предмет или товар не нужен, то от него нужно избавиться, а избавится жалко, так как в нашей стране «все всегда нужно» или «когда ни будь пригодится». Придется объяснять, что если предмет не нужен, его не обязательно выбрасывать, просто нужно найти для него соответствующее место, исходя из периодичности его использования, а если он ен используется именно в этой зоне, то передать в те зоны, где оно используется или может использоваться.
Так же большую проблему вносит отсутствие в компании программных продуктов, которые способствовали бы общению сотрудников участвующих в проекте с целью обмена опытом, так как зачастую информация о проблеме, выявленной на одном подразделении, и пример ее решения не доходила до другого подразделения. Следовательно, сотрудникам разных подразделений придется наступать на одни и те же грабли и искать пути решения самостоятельно.
— Каких результатов удастся добиться в первую очередь и быстро?
При правильном подходе, по окончанию первого и второго шага системы 5С уже увидите вовлеченность сотрудников и осознание необходимости преобразований. Если раньше сотрудники не задавались вопросом, почему какой-либо товар находится на хранении в той или иной зоне склада, и осуществляли свою работу, не задумываясь о трудоемкости, то после 2-х шагов сотрудники, участвовавшие в проекте, понимают почему, в каком количестве и как должен храниться товар, выявляют различного рода ошибки в процессах и самостоятельно инициируют работу по совершенствованию процессов, что в свою очередь снизит их трудоемкость в производственном процессе и возникновение возможных ошибок.
Первые несколько шагов очень сильно вовлекают и заинтересовывают сотрудников, и именно в этом заинтересованном состоянии необходимо держать сотрудников на всем этапе проведения проекта 5С, а после проведения необходимо позаботиться. Что бы полученные знания и навыки не забылись и вошли в привычку. Собственно, в следующих статьях мы детально и разберем каждый шаг в отдельности.
iambuilding.ru
Система 5S — эффективная организация рабочего места
Большинство сотрудников офисов, предпринимателей, бизнесменов и огромное количество других специалистов сегодня проводят большую часть дня за рабочим столом. Его организация очень важна для продуктивности сотрудника, потому что беспорядок или неправильная расстановка канцелярского оборудования помогает повысить функционал и эффективность работы. В этом вам поможет японская система организации рабочего места 5S.
Что такое система 5S и как ее используют?
Япония сегодня считается одной из самых развитых стран, которая имеет уникальную систему управления внутри компании, а также высокоэффективные производства. Но только по окончанию Второй мировой войны экономика Японии была в ужасном состоянии, потому что множество государств перестали с ней сотрудничать, промышленное производство было уничтожено, рабочих кадров очень мало, а сама страна была в долгах. Кроме того, существовали проблемы безработицы и дефицита товаров, поэтому жители страны начали требовать реформ и перемен.
Одним из таких предприятий, который уже находились на грани разорения, была компания Toyota. В этот период объемы сборки товаров упали до минимума, а количество сотрудников сократилось почти вдвое. И все изменилось практически за несколько лет, когда фирма начала зарабатывать несколько миллионов в год. Сегодня историю успеха Toyota ставят в пример другим корпорациям, которые начинают терять прибыль.
Первое, что сделали руководители и владельцы Toyota — изменили систему работы и разработали совершенно новые принципы. Именно благодаря им предприятие стало одним из самых успешных и крупных производителей автотехники в мире.
Один из новых механизмов, которые используются в Toyota, является методика организации рабочего процесса — это философия бережливого производства. Менеджеры этой компании выдали несколько книг и провели крупное исследование, после чего огромное количество других компаний тоже начали запускать такую же систему на своей фирме. В Toyota даже открыли специальный отдел, который занимался консалтинговыми услугами, чтобы помочь правильно организовать работу в других предприятиях. Кроме того, руководители отделов могут самостоятельно ознакомится с функционалом прямо в Toyota.
Владельцы компании утверждают, что они не создавали намеренно определенные принципы. Просто тогдашние руководители пытались срочно поменять систему производства, в результате чего появилась такая система. Из-за этого многие фирмы, которые пытаются наследовать механизм, не достигают таких успехов.
5 правил организации рабочего пространства
Основной сутью японской системы 5S является пять правил, которые используются владельцами рабочего стола. Весь механизм работы бережливого производства зависит от того, что каждый сотрудник прикладывает усилия для работы, при этом он реализует свои способности на полную и может сосредоточится именно на рабочем процессе.
5S состоит из пяти этапов.
Сортировка.
На рабочем столе размещается огромное количество предметов. Часто они могут быть незначительными или слишком маленькими и владельцу может казаться, что на самом деле со столом все в порядке. По сути предметы можно разделить на три категории:
- Необходимые — это те предметы, которые обязательно должны быть на вашем столе. Их нужно размещать под руками, чтобы быстро дотянуться.
- Нужны периодически — время от времени они могут понадобиться, но большую часть дня вам не нужно пользоваться этими вещами.
- Ненужные предметы — это те вещи, которыми вы вообще не пользуетесь, и они неизвестно как попали на ваш стол. Естественно, эту категорию нужно убрать из рабочего стола.
Соблюдение порядка.
После того, как вы убрали лишнее, нужно рассортировать то, что осталось. Более важные предметы должны располагаться так, чтобы вы не тратили время на поиск и могли на уровне рефлексов достать изделие.
Можете воспользоваться такими правилами, которые предлагают в Японии:
- Необходимые предметы лежат на видном месте.
- Нужные вещи лежат так, чтобы вы могли достать их рукой, при этом не поднимаясь с места.
- Предметы, которые используются постоянно, не берутся в руки тоже должны быть размещены так, чтобы в естественном положении их можно применять. Имеется в виду, например, клавиатура и мышка компьютера. Вы садитесь за стол и ложите руки так, чтобы они сразу легли на мышку и клавиатуру.
- В течение дня после использования нужные предметы должны ставиться обратно на свое место.
Содержание в чистоте.
Японцы советуют разбить рабочее место на несколько зон, каждая из которых будет отвечать за определенные изделия. Например, центр стола — для ноутбука или компьютера; левая часть — для канцелярии; правая — для документов.
Стандартизация.
Чтобы такие принципы производства были действительно полезными и эффективными для всего предприятия, нужно ввести их как стандарт. Абсолютно все сотрудники должны этого придерживаться, как и того, что на работу нужно приходить в 9 часов утра.
Лучшим вариантом будет сделать специальный документ, с которым ознакомятся все сотрудники. После этого периодически можно проверять результаты. Кроме того, нужно прояснить причину такого строгого контроля.
Совершенствование.
Любое действие и особенности поведения человека можно сделать привычкой. Конечным этапом 5S является доведение всех правил до того, чтобы они выполнялись на автоматизме.
Если раздумывать над правилами поведения и организации рабочего места, то по сути Toyota не придумала ничего нового. Но если их придерживаться, то можно заметить этот результат. Кроме того, самодисциплина на рабочем столе повышает производительность и в обычной работе.
Кол-во просмотров: 1 953
kompanion.online
Отраслевая энциклопедия. Окна, двери, мебель
Введение
Статья посвящена особенностям внедрения системы 5С в Российской Федерации. В ней раскрывается основа данной системы, выявляются эффекты, получаемые на этапах ее внедрения. В статье анализируются проблемы применения системы 5С на российских предприятиях, а также предлагаются меры, позволяющие устранить ошибки внедрения данной системы Ключевые слова: организация рабочего места, карта 5С, сортировка, систематизация, рациональное размещение, стандартизация правил, красные ярлыки, ненужные вещи
В настоящее время особую актуальность приобретает стремление предприятий производить все более усложненную продукцию и при этом затрачивать на нее как можно меньше средств. Это стремление находится также во взаимосвязи с такой составляющей, как конкуренция. Она стремительно набирает обороты, на рынок выходят все больше предприятий со своими инновационными идеями, чтобы не отстать, организациям необходимо внедрять в деятельность своих компаний различные новые методы или вводить уже проверенные и трансформировать их к своей среде. Японский опыт организации рабочего места на предприятиях является уникальным, он способствует как росту производительности, так и улучшению уровня качества продукции. Именно поэтому следует особо остановиться на японской системе организации рабочего места, которая называется «Система 5С». Существенной ее особенностью является возможность применения данного метода в условиях жесткого бюджетного ограничения. В основе Системе 5С лежат пять этапов, постоянное выполнение которых позволило японским предприятиям в кратчайшие сроки поднять экономику своей страны на высокий уровень, а компаниям, применяющим его, получать возросшую прибыль, при этом количество брака значительно сократилось, возросла производительность рабочих. Этапы в составе рассматриваемого метода включают в себя: 1) сортировку; 2) свои места для всего; 3) содержание в чистоте; 4) стандартизацию; 5) самодисциплина/совершенствование. Рассмотрим основные эти этапы более подробно.
Этапы внедрения 5С
Первый этап «Сортировка»
Сортировка означает освобождение своего рабочего места от всего, что не понадобится при выполнении текущих производственных или канцелярских операций. При выполнении этапа сортировки одна из основных составляющих заключается в определении тех деталей, предметов, которые впоследствии понадобятся при выполнении заказа и избавлении от ненужных вещей. Отметим, что, производя сортировку, сотрудники не только избавляются от тех изделий, которые точно не понадобятся, но также и от тех, на счет которых возникают определенные сомнения. Главное значение сортировки заключается в эффективном использовании ресурсов. Плюсы правильного выполнения данного этапа заключаются в следующем: – появление дополнительного места для хранения нужных деталей и инструментов; – снижение затрат на транспортировку ненужных деталей, для которых могла потребоваться какая-либо тара; – уменьшение времени на поиск требуемых вещей, что так же помогает сохранению благоприятной обстановки; – нужные вещи всегда будут находиться в рабочем состоянии, а их поломка будет обнаружена гораздо быстрее; – увеличивается производительность труда.
Следует отметить, что на рассматриваемом этапе одна из основных сложностей состоит в определении ненужных или просто лишних в данный промежуток времени предметов. Самый эффективный способ выявления потенциально лишних предметов и анализ их степени полезности называется «компания красных ярлыков». Суть его заключается в том, что те предметы, которые явно необходимы и не вызывают никаких в этом аспекте сомнений, оцениваются сразу. Если же предмет вызывает какие-либо сомнения, то на него вешается красный ярлык.
Для эффективного функционирования «компании красных ярлыков» необходимо так же осуществлять документирование, для каждой компании оно индивидуально. Примером может служить ведение журнала учета или хранение всей информации в компьютерной системе организации. Данные результаты, их анализ позволят наглядно увидеть те улучшения, к которым привело внедрение «красных ярлыков». Остановимся более подробно на возможных проблемах, которые могут возникнуть на первом этапе внедрения 5С:
а) полки и другие виды помещений, куда были сложены ненужные предметы, разделили рабочее пространство, что впоследствии стало причиной неудобства для взаимодействия рабочих; б) для поиска различных деталей стало уходить больше времени; в) содержание ненужных вещей приносит большие затраты; г) накапливается много хлама, что в свою очередь отражается на работе в целом и другие. Если при проведении сортировки были выявлены одна или несколько выше представленных проблем, то необходимо еще раз провести данный этап метода, выявив при этом причины, породившие данные проблемы.
Второй этап «Свои места для всего»
После успешного завершения первого этапа на предприятии, внедряющем рассматриваемую систему, стоит перейти ко второму, который называется «свои места для всего». Суть его заключается в том, чтобы предметы располагались таким образом, при котором их можно было бы легко использовать, а маркировка была такой, чтобы любой рабочий мог быстро найти нужную ему вещь, затратив минимум времени. Чаще всего потери времени происходят при: передвижении, отсутствии техники безопасности, поиске предметов, от излишков запасов, при работе с некачественными изделиями. Это позволяет сделать вывод, что главная особенность данного этапа состоит в сокращении времени на поиск нужного предмета рабочим, что впоследствии скажется на продуктивности работы. Выбор лучшего расположения для различных инструментов исходит из расчета минимум движений для взятия и использования предмета, что сокращает потери. Потери – это операции, которые требуют затрат времени и ресурсов, но не повышают ценности товара или услуги для потребителя. Поэтому удобное расположение вещей позволяет снизить потери времени, для этого на предприятиях часто используется карта 5С. Сущность карты 5С состоит в том, что она является механизмом, который помогает оценить в настоящее время местонахождение различных приборов, вещей, необходимых для работы, и выбрать наиболее рациональное расположение для этих предметов. Ее можно разделить на 2 части. Для наглядного примера приведем карту 5С с разметкой машинных операций до применения системы 5С, которая представлена на рис. 1.
Рис.1 Карта 5С с разметкой машинных операций до применения системы 5С
Как видно на рис. 1, в первую часть карты входит то расположение предметов, которое было до внедрения данной карты, теперь рассмотрим карту после внедрения 5 S, которая представлена на рис. 2.
Рис. 2 Карта 5С с новой разметкой машинных операций
На рис. 2 видно, что новая разметка структурировала этапы цикла машинных операций, сократив тем самым время на их выполнение и увеличив производительность. Итак, можно сделать вывод, что второй этап системы 5С позволит сократить время на выполнение операций, внесет строгую последовательность, которая позволит избежать хаоса на рабочем месте, тем самым увеличив производительность.
Третий этап «Содержание в чистоте»
Перейдем к третьему этапу, который называется содержание в чистоте. Применять его следует только после осуществления второго, так как они тесно взаимосвязаны между собой. Сущность систематической уборки состоит в постоянном поддержании чистоты, как на рабочем месте, так и отдельных вещей в частности. Отметим плюсы данного этапа: – появление удовлетворенности работника своим рабочим местом; – полная готовность предметов, которые нужны для выполнения работы; – повышается безопасность рабочего места; – снижается вероятность брака; – постоянный технический осмотр увеличивает время работы без поломок оборудования. Систематическая уборка рабочего места является обязанностью всех сотрудников, которые на нем работают. Для ее проведения выделяется определенное время, назначенное руководством. После того как уборка вошла в систематическую фазу, следует внедрить проверку и оборудования. Для этого следует определить объект, на который будет направлено данное действие (например, режущий станок), далее сотрудников, которые непосредственно этим будут заниматься, после этого следует подготовить инструменты для уборки, а в завершение ввести систематическое ее выполнение. Итак, подводя итоги третьего этапа, следует отметить, что целью уборки является содержание в чистоте и отличной работоспособности всего, что используется или может быть применено для выполнения поставленных производственных задач. Данный этап нацелен на систематизирование содержание не только рабочего места в чистоте, но и на систематическую проверку оборудования, что позволяет повысить безопасность на рабочем месте, время работы оборудования, а также уменьшает количество производимого брака.
Четвертый этап «Стандартизация»
Рассмотрим следующий этап – стандартизация, сущность которого заключается в организации унифицированного подхода, который будет понятен всем работникам и будет простым в использовании. Для успешной стандартизации необходимо, чтобы была включена постоянная сортировка, самоорганизация и систематическая уборка. Следует отметить, что для каждого рабочего места необходимо иметь рабочие стандарты, рабочие инструкции наглядны, понятны, облегчают и работу, и обучение новых сотрудников. Кроме того, следует сделать так, чтобы инструкции находились непосредственно на рабочем месте, т. е. там, где выполняется работа, чтобы при необходимости сотрудник мог всегда к ним обратиться. Все инструкции следует составлять так, чтобы они были исполнимы. Таким образом, четвертый этап включает в себя несколько шагов, таких как определение обязанностей, по выполнению первых трех этапов системы 5С, следующий шаг состоит во внедрение разработанной стратегии в график работы сотрудников без ущерба для выполняемой ими работы, последний же этап заключается в контроле за исполнением. Данный этап позволяет наладить работу предыдущих ступеней и при этом отслеживать какие-либо нарушения или отставания.
Пятый этап «Самодисциплина/ совершенствование»
Пятый этап системы 5С называется самодисциплина/ совершенствование. В отличие от первых четырех, на нем результаты не так очевидны и не поддаются измерению. Стремление работников к совершенствованию возможно лишь поощрить, создавая условия для стремления к этому. Примером условий стимулирования данного этапа может служить: понимание сотрудниками необходимости и эффективности внедрения системы 5С, выделение времени на обдумывание и реализацию замыслов, помогающие внедрению 5С, поощрение со стороны руководства. В табл. 1 представлены эффекты, получаемые на этапах внедрения 5С:
Таблица 1.
Виды эффектов при внедрении системы 5С
Проблемы при внедрении системы 5С
В настоящее время можно утверждать, что данная концепция организации рабочих мест успешно внедряется во многих странах мира, но на российских предприятиях, особенно это касается предприятий Пензенской области, редко применяется. Одной из основных причин отказа российских предприятий от внедрения системы 5С является неправильное толкование и реализация данной концепции руководителями или персоналом, рассмотрим их главные ошибки. Так, на первом этапе реализации метода системы 5С могут возникнуть следующие проблемы: – невысокий приоритет, который ставят руководители на предприятиях; – контроль внедрения находится не в тех руках; – неэффективность из-за направления деятельности предприятия; – нечеткое понимание действия системы 5С и ее выгод; – отдельные ошибки реализации. Остановимся подробно на каждой из этих проблем в отдельности. Во-первых, невысокий приоритет для руководителей. Управленец всегда должен понимать, что на его поведение равняются, а его отношение к делу анализируется работниками более низкого звена, ведь если начальник не видит в этом внедрении какой-то необходимости или относится к ней незаинтересованно, то и работники будут относиться к этому так же. Кроме того, в настоящее время внедрение зарубежного опыта становится модой, часто выполняется лишь для галочки, поэтому некоторые руководители даже не считают нужным пройти самим эти курсы, а от того, что их пройдут лишь работники, эффективности будет мало. Для реализации этапов системы 5С требуется выделение времени для их реализации, порою же руководители пренебрегают этим. Во-вторых, при внедрении системы 5С следует не забывать о систематическом контроле всех этапов, но при распределении и назначении этой обязанности необходимо помнить такие моменты, как есть ли у этого работника полномочия для осуществления этой деятельности и ресурсы, чтобы реализовать контроль своевременно, ведь именно бюрократические проволочки даже внутри среднего предприятия бывают очень затяжными. Третья основная проблема для предприятий состоит в том, что не для всех сфер деятельности будет одинаковый результат, так, например, для организаций, работающих в металлургической области эффективность системы 5С, будет очень незначительной, так как для ее высокого функционирования достаточно поддержания в рабочем состоянии оборудования, а другие составляющие будут незначительно влиять на общую работу в целом. Нечеткое понимание действия системы 5С и ее выгод заключается в нежелании сотрудников переходить на данную модель, причин можно назвать много, но главная состоит в том, что не было уделено достаточно внимания просвещению персонала о данной модели, ее плюсах для каждого конкретного работника и всего предприятия в целом. К отдельным ошибкам реализации относятся уже более частные проблемы. Например, утрировав этап избавления от ненужных вещей, работников заставляют избавляться практически от всех предметов, которые находятся на рабочем месте, тем самым как бы поддерживая иллюзию наведения порядка, а на самом деле без маленьких мелочей работать становится неудобно, что впоследствии сказывается на отношении в целом к системе 5С. Для того чтобы данная система действительно работала в российских компаниях, которые начинают ее у себя внедрять, надо понять, что главное – это желание сотрудников и особенно руководства применить ее для эффективности производства, а не просто для галочки.
Заключение
В заключение выделим основные меры, позволяющие устранить ошибки внедрения системы 5С на российских предприятиях: 1) руководителю следует показать свою личную заинтересованность во внедрении данной системы; 2) на совещаниях необходимо проводить анализ хода внедрения системы на предприятии; 3) выявление сотрудников, которые больше всех внесли улучшений в данную систему и поощрение их; 4) контролировать просвещение новых сотрудников предприятия, связанное с осуществлением системы 5С; 5) работник на предприятии, понимая то, что при такой организации его рабочее место будет более удобно и безопасно, станет стремиться к совершенствованию этой системы, проявляя инициативу и доводя ее до сотрудников и руководителей; 6) сотруднику или нескольким работникам, на которых возложили обязанность контролировать осуществление данного метода, следует со всей ответственностью подойти к данному заданию, выявлять те проблемы, которые существенно снижают эффективность внедрения, а также доводить свой анализ до руководства, например, высылая результаты им на электронную почту. Анализ системы 5С позволяет утверждать, что ее эффективное внедрение на российские предприятия возможно, ведь самым важным в данной системе является желание и понимание всех сотрудников различных занимаемых рангов тех выгод, которые может принести данная система конкретно для них и для всего предприятия в целом. При этом никогда не надо останавливаться на достигнутых результатах, всегда стремиться к совершенствованию и систематизации.
Литература:
1. Хироюки Х. 5 S для рабочих: как улучшить свое рабочее место. – М.: Институт комплексных стратегических исследований, 2006. С. 32. 2. Тэппинг Д., Данн Э. Бережливый офис. Устранение потерь времени и денег. – М.: Альпина Паблишер, 2012 3. Растимешин В. Е., Куприянова Т. М. Упорядочение / 5 S – система наведения порядка, чистоты и укрепления дисциплины с участием всего персонала
Вклад участника:
Рогозик Денис Викторович
www.wikipro.ru
5S на транспорте — 1 шаг 5С и введение
Рис. 1. Лестница создания эффективного рабочего места.
Система устанавливает пять шагов, выполнение которых направлено на создание условий для стабильного оптимального выполнения операций, поддержание порядка, чистоты, аккуратности, экономии времени и энергии для повышения производительности, предотвращения несчастных случаев, снижения загрязнения окружающей среды.
Таблица 1
Основные принципы системы 5С
Принцип |
Содержание работы |
1. Сортировка: оставьте только нужное (ККЯ) |
Все предметы разделяются на три категории: нужные, не нужные срочно и ненужные. Нужные сохраняются на рабочем месте. Не нужные срочно располагаются на определенном удалении от рабочего места или хранятся централизованно Ненужные удаляются. |
2. Свои места для всего: каждой вещи свое место |
По отношению к нужным предметам и предметам не нужным срочно вырабатываются и реализуются решения, которые обеспечивают: ·быстроту, легкость и безопасность доступа к ним; ·визуализацию способа размещения и контроля наличия, отсутствия или местонахождения нужного предмета; ·свободу перемещения предметов и эстетичность рабочего места (автомобиля). |
3. Содержание в чистоте: рабочее место в исправном, подготовленном к работе состоянии |
Тщательная уборка и очистка рабочего места (автомобиля) и оборудования. Фиксация и устранение неисправностей. Выявление источников загрязнения, труднодоступных и проблемных мест. Выработка и реализация мер по уборке труднодоступных мест, ликвидации источников проблем и загрязнений. Выработка правил проведения уборки-проверки, чистки оборудования, смазки. |
4. Стандартизация процедур поддержания чистоты и порядка |
Фиксация в письменном виде правил и стандартов выполнения рабочих операций, направленных на: удаление ненужного, рациональное размещение предметов, уборку, смазку, проверку. |
5. Самодисциплина: стимулируйте поддержание порядка |
Закрепление сфер ответственности за каждым водителем (объекты внимания и основные обязанности по их поддержанию в нормальном состоянии). Выработка у водителей правильных привычек, закрепление навыков соблюдения правил. Применение эффективных методов контроля – чек-лист. |
В целом применение системы 5С позволяет создавать эффективные рабочие места, что в дальнейшем дает экономию средств, улучшает качество, поднимает эффективность перевозки товара, повышает уровень производительности и безопасности труда.
Система 5С направлена на следующие объекты:
— Внешний вид водителя;
— Рабочие зоны:
— Салон автомобиля
— Кузов автомобиля
— Внешнее состояние автомобиля
— Техническое состояние автомобиля
— Предметы у водителя и в зоне:
— Спецодежда, документы, электронные устройства.
— Предметы и оборудование, необходимые для выполнения работы (ККМ, сейф, погрузочно-разгрузочное оборудование, стяжные ремни, противооткатное устройство)
— Предметы, необходимые по правилам дорожного движения (аптечка, огнетушитель, знак аварийной остановки и т.д.)
— Средства для ремонта автомобиля (запасное колесо, домкрат, балонный ключ)
4. ОРГАНИЗАЦИЯ РАБОТ ПО ВНЕДРЕНИЮ СИСТЕМЫ 5С
4.1 Перед началом работы необходимо определить:
— Цель работы
— Руководителя работ
— Состав рабочих групп
— План-график проведения встреч рабочих групп
4.2 Ответственность за внедрение системы 5С в филиале возлагается на Заместителя директора филиала. Ответственность за проведение и поддержание системы 5С на грузовых автомобилях возлагается на сотрудника, ответственного за выпуск автомобиля на линию.
4.3 Рекомендуемый состав рабочей группы:
— Заместитель директора филиала;
— сотрудник, ответственный за выпуск автомобиля на линию;
— водитель/водители.
Примечание: состав группы может быть иным, в зависимости от организационной структуры подразделения.
5. ШАГ №1 СИСТЕМЫ 5С: СОРТИРУЙТЕ: ОСТАВЬТЕ ТОЛЬКО НУЖНОЕ
5.1. Цель первого этапа 1С – определить необходимые для рабочей деятельности предметы, освободить рабочее пространство от ненужных предметов, создать предпосылки для организации визуального управления и стабилизации процесса.
5.2. В случае, если чистота и санитарное состояние автомобиля находятся на невысоком уровне, целесообразно начать с генеральной уборки, которая позволит быстро освободиться от существующей части грязи и мусора, неприятных запахов. Кроме того, самому водителю необходимо привести себя в порядок и свой внешний вид. Затем приступать к реализации первого шага системы 5С.
Схема проведения 1С представлена в таб. 2.
Таблица 2
№ этапа |
Этап |
Название этапа |
1.1 |
Подготовительный |
Определение графика проведения Сортировки |
Определение перечня работ |
||
1.2 |
Определение критериев необходимости предметов в автомобиле и у водителя |
|
1.3 |
Фотографирование водителя и автомобиля |
|
2.1 |
Реализация |
Идентификация предметов у водителя и в автомобиле |
2.2 |
Оценка степени необходимости каждого предмета, принятие решений |
|
2.3 |
Документирование результатов 1С, фиксирование списка необходимых предметов в контрольный листок |
|
2.4 |
Удаление предметов, по которым принято соответствующее решение, из автомобиля и у водителя |
|
Перемещение предметов, по которым принято соответствующее решение |
5.3.1. Подготовительный этап.
5.3.1.1. Рабочая группа проводит организационное совещание, на котором:
— разрабатывает график проведения 1С;
— участниками рабочей группы изучаются теоретические и методические материалы. При необходимости для проведения обучения руководитель группы приглашает кайдзен-менеджера если таковой сотрудник имеется в компании или на предприятии.
— Определяются способы и порядок удаления предметов.
Примечание: рекомендуемые способы удаления предметов:
• Выбросить (самое последнее)
• Передать другим водителям
• Продать
• Передать другому подразделению
Также рабочая группа перед началом шага 1С разъясняет водителям цели и задачи 1С и системы 5С в целом.
5.3.1.2. Рабочая группа определяет критерии необходимости предметов в автомобиле и у водителя. Рекомендуется за основу взять следующие три критерия:
— Необходимость предмета при выполнении текущей деятельности. Это могут быть как предметы, используемые непосредственно в работе водителя (стяжные ремни, документы на груз, перчатки, ручка, мобильный телефон и т.д.), так и предметы первой необходимости (аптечка, огнетушитель, знак аварийной остановки). Если предмет не нужен, он должен быть удален из рабочей зоны (кабина или кузов) и удален у водителя;
— Частота использования. Если предметом пользуются редко, то его можно хранить вне рабочего места;
— Количество предметов, необходимых для текущей деятельности. Если нужно ограниченное количество предметов, излишки можно удалить или хранить вне рабочего места. К примеру, если положено 4 стяжных ремня, то должно быть 4 (максимум 6 – на случай дополнительного крепежа, поломки или повреждения) стяжных ремня. Также и с пишущей ручкой. Нет необходимости хранить несколько ручек в разных частях салона (двери, бардачок, панель приборов, подлокотник и др.). Достаточно 1-2 ручек для оформления документов.
5.3.1.3. Рабочая группа фотографирует текущую ситуацию в автомобиле и самого водителя. Фотографирование автомобиля должно проходить со всех сторон, включая рабочие зоны (салон и кузов). Также фотографируется водитель спереди и сзади во весь рост. Фотографии сохранены в папку с указанием даты фотосъемки.
5.3.2. Этап реализации
5.3.2.1. Рабочая группа проводит идентификацию предметов в автомобиле и у водителя, а также определяет степень необходимости этих предметов и в соответствии с этим принимает решение об их дальнейшей судьбе:
— оставить предмет там, где он находится
— изменить количество
— переместить предмет на новое место в пределах автомобиля;
— утилизировать;
В результате должен быть сформирован список необходимых предметов всех рабочих зон и у водителя, который используется для формирования Контрольного листка (см. п. 5.4.3)
5.3.2.2. Удаление ненужных предметов.
— Выявленные лишние предметы должны быть удалены из автомобиля сразу же после принятия решения о способе удаления.
Примечание: Возможные рекомендуемые способы удаления предметов:
• Выбросить – для выявленных лишних предметов, не представляющих ценности.
• Передать другим подразделениям или водителям – для выявленных лишних предметов, представляющих ценность, и необходимых на других участках.
• Продать – для выявленных лишних предметов, представляющих ценность, но не нужных для выполнения рабочих операций.
5.3.3. Контроль эффективности первого шага системы 5С
Контроль эффективности внедрения первого шага системы 5С осуществляется при помощи «Контрольного листа по проверке эффективности внедрения первого шага системы 5С». Контрольный лист 1-го уровня (аудит выполняется самим водителем) должен храниться в салоне автомобиля в лотке или папке.
Эффективность внедрения первого шага оценивается по автомобилю и водителю в целом. Наличие правил отнесения предметов к нужным, кол-во предметов и место их нахождения.
iambuilding.ru
Внедрение 5S — оптимизация рабочего пространства
Практическая часть
Как сделать 5S рабочих мест в офисе:
1
Вытащить всё со своих мест, в том числе из всех закоулков. (Для крупных помещений можно частями, но нежелательно).
2
Вытереть, вымыть, удалить грязь.
3
Выкинуть лишнее, или отложить его в зону карантина, или пометить «красным ярлыком», если предмет пока некуда переместить и предмет на виду.
Идея «внедри-сегодня»:
зона карантина
Нужно: 1 коробка, 3 минуты (офис) либо 1-2 квадратных метра, 5 минут (производство).
Помещайте в зону карантина предметы, которые неизвестно, нужны или нет. Если в течение 1 месяца предмет не потребовался — его надо удалить.
4
Выделить «зону хаоса»
Идея «внедри-сегодня»:
Зона хаоса
Нужно: любой способ отмаркировать место (например, изолента или открытая коробка).
Выделите место и разводите бардак только там. Со временем уменьшайте это место. Важно! Не в ящике стола!!! — надо там, где бардак виден.
5
Запланировать, где что будет лежать. Можно сразу делать по частям (может быть придется переделать) или сначала обсудить общее расположение предметов и нарисовать общий план. Это уж как удобнее конкретным людям. Размещение предметов нужно обсудить со всеми, кто будет пользоваться. Этот момент -самое то, чтобы передвинуть также столы, шкафы, зоны. Выслушайте идеи всех участников обсуждения. очень часто в коллективе гораздо больше хороших решений, чем кажется.
Важно: планировать должны те, кто будет пользоваться. Дело не в том, чтобы всё внешне смотрелось красиво, а в том, чтобы было максимально удобно использовать, то есть для каждой вещи нужно найти наилучшее место.
Это значит, что своё индивидуальное рабочее место человек должен планировать сам. И ничего страшного, если у каждого работника оно будет организовано по-разному.
А вот например общий шкаф с документами, принтер, рабочее место, которым пользуется несколько человек и т.п. — нужно обсудить вместе. Заранее выберите руководителя, который будет принимать решения, если консенсус не получится.
6
Разложить вещи примерно так, как будет, и по мере раскладывания подправить план.
Советы
• Зоны удобно выделять цветной изолентой. Почему? Изолента удобна, чтобы перемещать зоны, пока они не устоялись. Да, может так оказаться, что то, что придумали вначале, окажется не наилучшим. Зачем нужна зона? Чтобы было видно, что предмет на месте.
• Когда много бумаг, скрепляйте степлером или скрепкой бумаги по одной теме и надпишите их. Так вместо 100 бумаг получилось 14 кучек по 14 вопросам, психологически гораздо легче.
• Что чаще используется — лежит ближе. Обратите внимание также, на какой высоте это размещено (не надо тянуться), под правую или под левую руку повешено.
• Хранение в точке использования — это идеальное решение для часто используемых предметов (да и вообще для всех, если получится).
7
Сделать маркировку (создайте файл, которым будете всегда пользоваться, тогда у вас будут одинаковые шрифты и не придется нигде записывать, какой у них размер и пр.)
Советы
• Чтобы не портить стену, используйте белый малярный скотч, и также можете прикрепить к стене бумагу, чтобы нанести на неё контуры предметов. Белый малярный скотч подойдет и для нанесения надписей на стену. В этом случае, пока всё не устоялось, Вы сможете поменять местами предметы, передвинуть надпись.
8
Сделать «приспособления» там, где они нужны (например, разграничители, коробки и пр.).Со временем вы сможете их улучшить и сделать более красивыми. На начальном этапе достаточно вырезать из картона и склеить скотчем, так как первое время Вы будете их перемещать и менять.
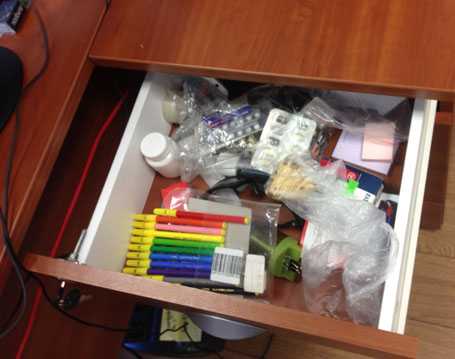
До:

После:
Советы
• Не страшно, если сначала Ваши «приспособления» будут выглядеть грубовато. До того как их «изваять в камне», нужно будет их переделать раз по 5 🙂
• Контурные формы можно вначале вырезать из картона, а затем уже из фанеры
• Вам пригодятся картонные коробки и пластиковые контейнеры
• «Удобно» всегда лучше, чем «красиво». Экономьте каждое движение, и тогда Вы действительно будете убирать предметы на место.
8
Пусть каждое рабочее место будет индивидуальным. Не пытайтесь все места сделать одинаковыми, каждый делает под себя. Пусть предметы будут там, где Вам нужно, но пусть у них будет продуманное место.
Важно! Несоблюдение этого принципа в разы повышает сопротивление сотрудников. И наоборот, соблюдение этого принципа может подтолкнуть работников найти интересные решения, сравнивать между собой и в целом гордиться сделанной работой.
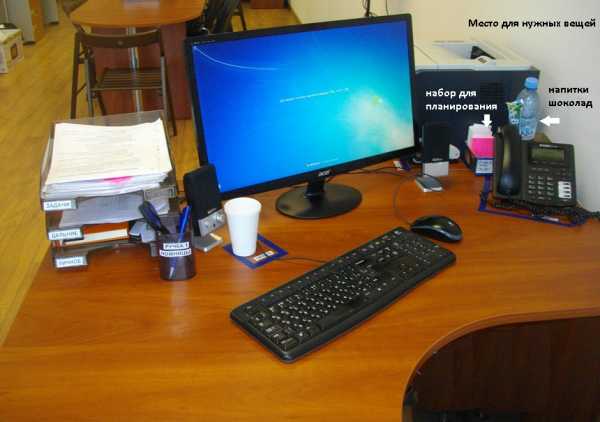
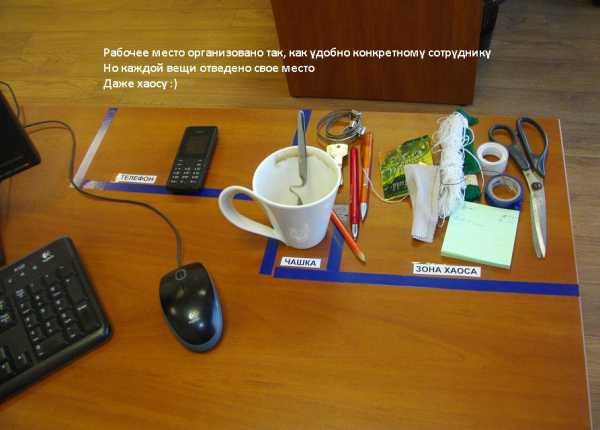
9
Надпись учит нас ставить предмет на место, поэтому нужна!
Кажется, глупо писать «телефон», «чашка». Но, например, раньше я клал сумку куда попало, она все время мешала, иногда терялась. Затем я выделил место для нее, но не сразу привык класть её туда. А когда есть надпись (или другая маркировка, например, контур предмета) — сразу видно, куда положить, и сразу видно, если что-то не на месте. Можете сделать надпись так, чтобы предмет, стоящий на месте, закрывал её.
Когда речь идет о большом количестве предметов, можно использовать не надпись, а их контуры, или выдавленные в соответствующем материале формы и т.п.
Особенно это актуально, когда многие люди используют один комплект инструмента или других каких-либо вещей.
Обязательно кладите каждый предмет на отмаркированное место. Это совсем не долго, если места эти продуманы и удобны. Если предмет не ясно, куда положить, положите его в зону хаоса.
10
Закрепите провода, а также всё, что может упасть, разбиться, нанести травму.
11
Содержите свое место в чистоте! Это займет всего несколько минут в день, а настроение будет гораздо лучше.
12
Стандарт рабочего места и ответственный за содержание рабочего места (или другой зоны, например, шкафа с образцами и т.п.) позволяют проверять друг друга. Стандарт может выглядеть в виде фото с изображением предметов так, как они должны быть расположены, или схемы. Например, так:
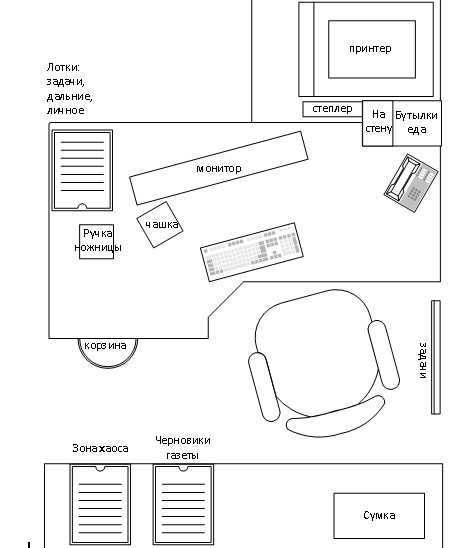
13
Регулярно проводите аудиты друг у друга, и ставьте оценку по результатам. Поощряйте лучших.
Для рабочих мест складских помещений и производства применяется несколько более расширенная технология, об этом будет рассказано в конце статьи.
spb-progressor.ru